Our industry-leading, high-speed industrial robots include high-payload, extended-reach, ultra-maneuverable seven-axis and unique 15-axis dual-arm robots.
Yaskawa: Sigma-X servo systems for the electronics industry
Smart features for high-precision production and handling applications
Yaskawa's new Sigma-X high-end servo system extends the technical possibilities in semi-conductor production: specialist machine and system manufacturers and users in the electronics industry will all benefit from even smarter features.
To comply with sector-specific regulations, such as SEMI S2 and SEMI S8, the machines and systems used to manufacture semi-conductors must fulfill the most stringent precision standards. The performance requirements for the servo motors used in this industry are therefore correspondingly exacting. This is especially true for pick & place applications, such as those involved in circuit board assembly, wafer-handling and other technically complex automated tasks, such as wet etching. Reliability and availability are the decisive factors here, because down-times can cost a great deal of time and money. For this reason, servicing and maintenance tasks should be straightforward and possible to perform in a timely manner. Another critical factor is a long service life, to ensure a good return on initial investment costs.
Mastering complex applications
Servo systems have to handle a number of challenging tasks at the same time, for example, during crimping, when two components are joined together by a process of plastic deformation: they must maintain a constant, exact pressure at all times, and distribute this pressure across a number of synchronized axes. A further requirement is that movement can be stopped at any position, while ensuring that the stability of the process as a whole remains the same throughout the entire production cycle.
In coating processes, as a second example, plates that are rotating at high speed are sprayed evenly with liquid. To achieve a precise result, the ripples in the speed must be adjusted and reduced in a specifically targeted way. Tailor-made solutions can also be developed for other specific applications and to meet other exacting challenges.
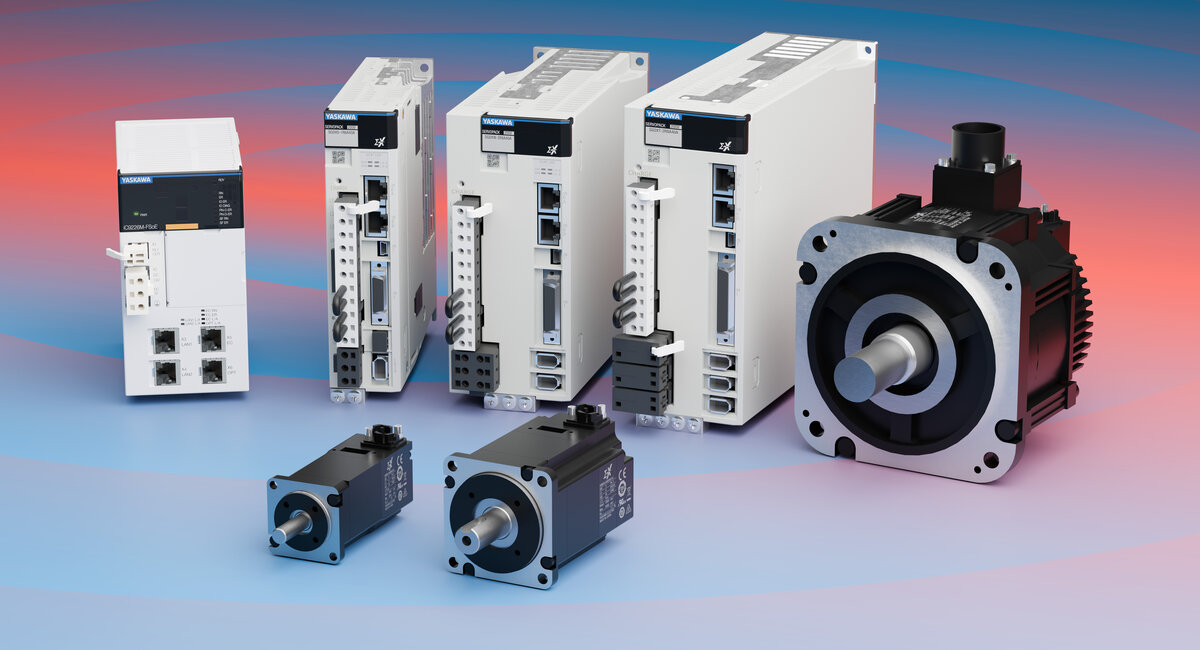
Sigma-X High-End servo system
Yaskawa‘s new Sigma-X high-end servo system has a range of smart features, such as optimized torque compensation, automatic load adjustment, vibration suppression and synchronized axis control, that enable it to handle these specific challenges.
The aim of these extended developments was to improve the competitiveness of machine manufacturers and users alike, and enable them to retain their technical lead over their competitors: The very compact servo motors allows for the design of ever smaller machines. At the same time, the versatile tuning functions can be learned and applied very easily.
The system automatically detects, and then counters, machine-generated vibrations and resonances. The acceleration sensors integrated in the new servo motors can now detect unwanted machine conditions at an early stage. The servo amplifier also provides users with a range of helpful information such as electrical consumption data, current performance and temperature reserves, maintenance cycle indicators, vibrations and much more. The machine’s performance capability can therefore be analyzed and optimized on an on-going basis to ensure maximum operational availability.
Smart features
The new smart features have been designed so that operational performance and control can be optimized reliably, whilst also increasing productivity and improving system availability. In turn, all of this goes improving competitiveness. For this reason, Yaskawa has once again improved these intelligent functions, even when compared with its previous Sigma-7 series servo motors: For example, Sigma-X can now control torque even more accurately, and with even greater precision, than its predecessor. In the manufacture and processing of wafers, the ability to suppress vibrations during polling is especially important. Sigma-X is also in use in other specific applications such as wafer-handling, wire bonding, wafer wet etching, path tracking, grinding polishing, wafer dicing or cutting machining.
Yaskawa's servopacks can now suppress vibration frequencies even more than before. This functionality has been available since Sigma-V. The Sigma-7 series enables two vibration frequencies to be suppressed at once. Consequently, the mechanism does not need to be more rigid and material costs are reduced.
A different function can use multiple parametrized set values as input signals for compensating for speed ripple. On Yaskawa motors, this function is activated as standard. For all other motor types, this function can be activated and adjusted with the SigmaWin+ software.
In the case of applications, such as robots and transfer systems, in which the load (moment of inertia) varies greatly, positioning usually takes longer. Thanks to the load fluctuation compensation adjustment function, positioning always takes the same amount of time, provided that the load fluctuations are within ±500 % of the set reference value.
The Yaskawa servopack can identify errors in movement patterns, so preventive maintenance can be performed. Multiple tracks in a particular movement pattern are recorded. They are analyzed, saved in the servopack and continually compared with the current movement. When a particular threshold is exceeded, the servopack issues an alarm.
Yaskawa as solution provider
The Sigma series of high-end servo systems from Yaskawa have proven themselves over the decades in multitude of application areas, not only in semi-conductor manufacturing systems, but also in packaging machines, in timber processing plants and in digital printing machines. With Sigma-X, the latest evolution of the Sigma series, Yaskawa is once again setting new benchmarks for performance and ease-of-use. These new products can also be used to replace existing Sigma-7 systems.
At present, the new system is available in models for 200 V, from 50 Watts to 15 kW. Models for 400 V will follow in the near future. Servo amplifiers for the simultaneous connection of up to three servo motors are also now available, as well as models with special firmware for use in gantry systems. Analog/Pulse, EtherCAT and Mechatrolink-4/III interfaces can all be used. All servo amplifiers are fitted with Safe Torque Off (STO) as a functional safety feature.
Sigma-X components have been specially designed to work together flawlessly, ensuring optimal technical performance. They are all integrated in the new iCube control platform. The iC9226 controller works with Yaskawa‘s TRITON industrial chip and can control up to 64 servo axes synchronously. It can be programed using the iCube Engineer software tool and can be fitted with, or without an integrated FSoE Safety Master.
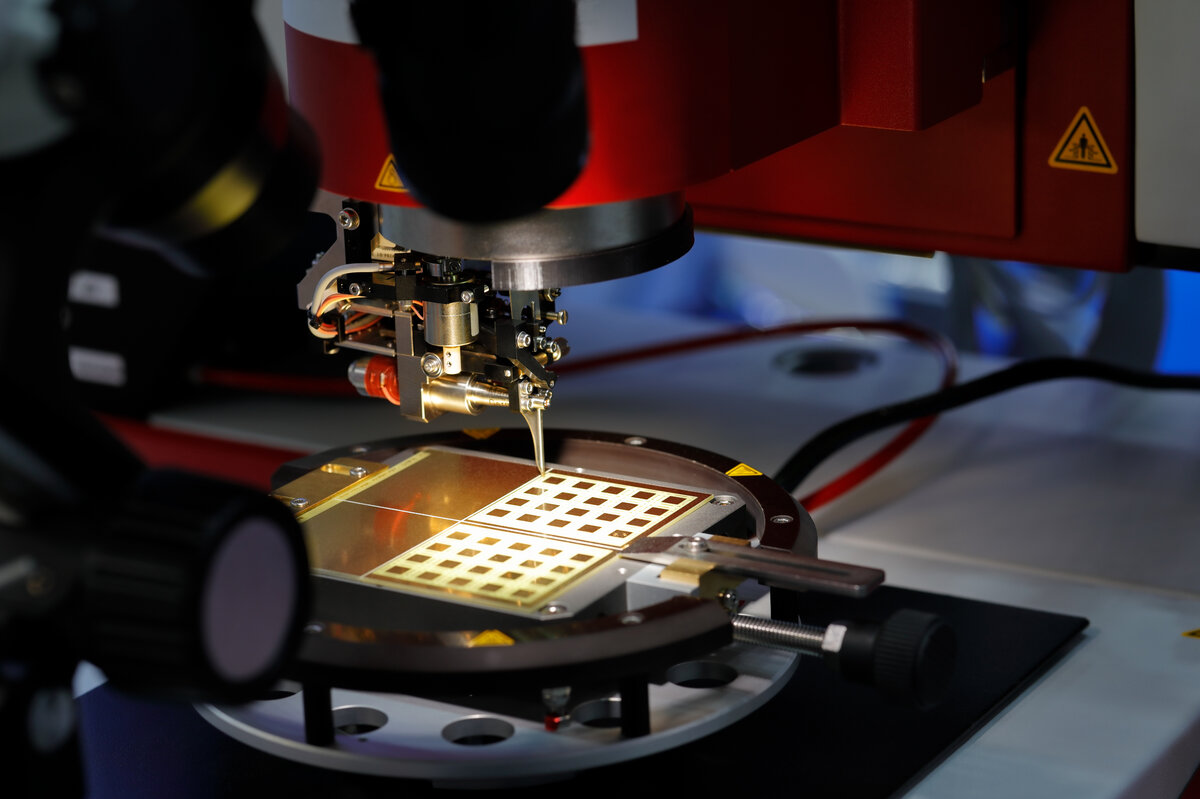