Our industry-leading, high-speed industrial robots include high-payload, extended-reach, ultra-maneuverable seven-axis and unique 15-axis dual-arm robots.
Seam polishing robot for Bomag drum roller production
Welding seams in perfection
Bomag uses the latest technology in the production of rolling elements for single drum rollers. Many of the steps are carried out by robots - now including the cleaning and polishing of the weld seams. The result is a perfectly rounded weld seam that weighs tons. This creates the best conditions for smooth surfaces in road construction.
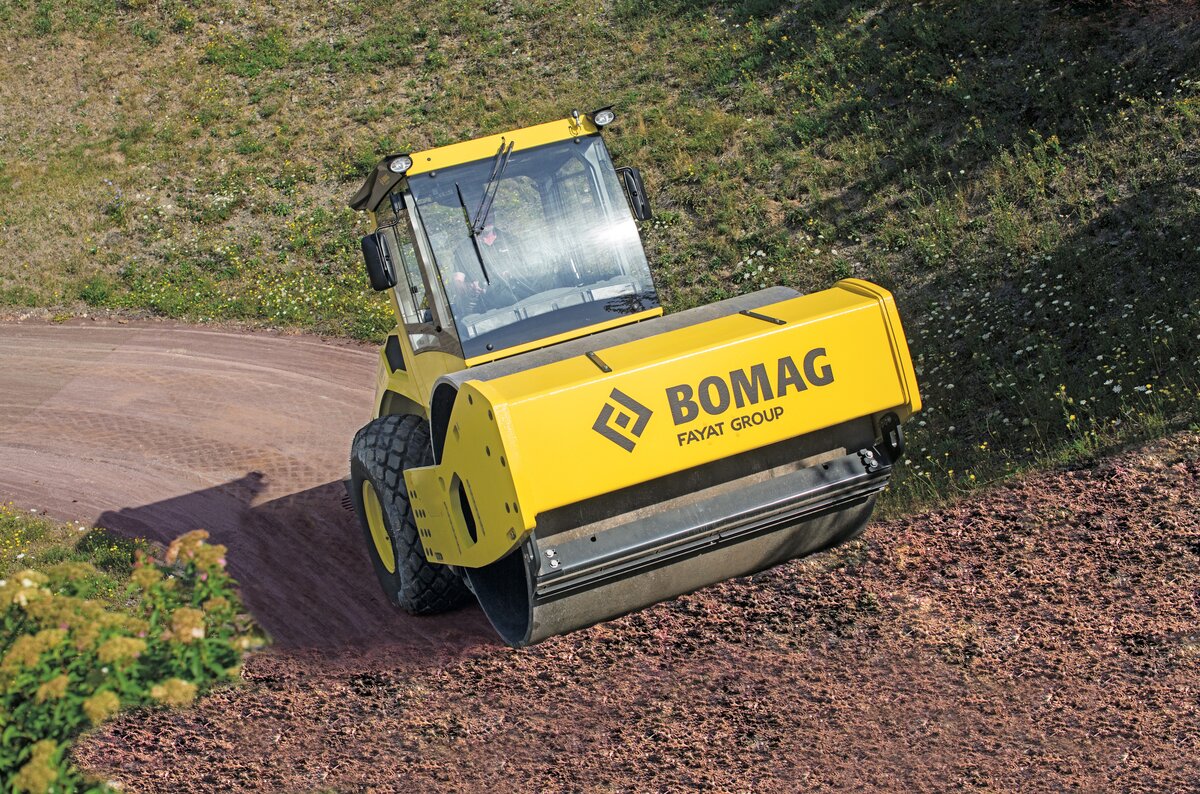
The drums used by Bomag's mobile machines to compact the subsoil for road construction weigh up to twelve tons and are aided by vibration technology. In this demanding area of construction machinery technology, the company, headquartered in Boppard am Rhein, is the world market leader and in 2013 commissioned a new plant for the drum production of single drum rollers.
In the production process up to 60 mm thick sheet metal - some of which consists of extremely wear-resistant Hardox steels - are first rounded, requiring bending forces of up to 6,000 tons. Then comes the fully automated welding of the longitudinal seam as well as the dished plates, i.e. the side parts of the single drum rollers. Then the longitudinal seam on the single drum roller must be cleaned up and polished with high precision. Any out-of-roundness, however slight, would impair the quality of the planum, which is the technical term for the substructure of the asphalt layer.
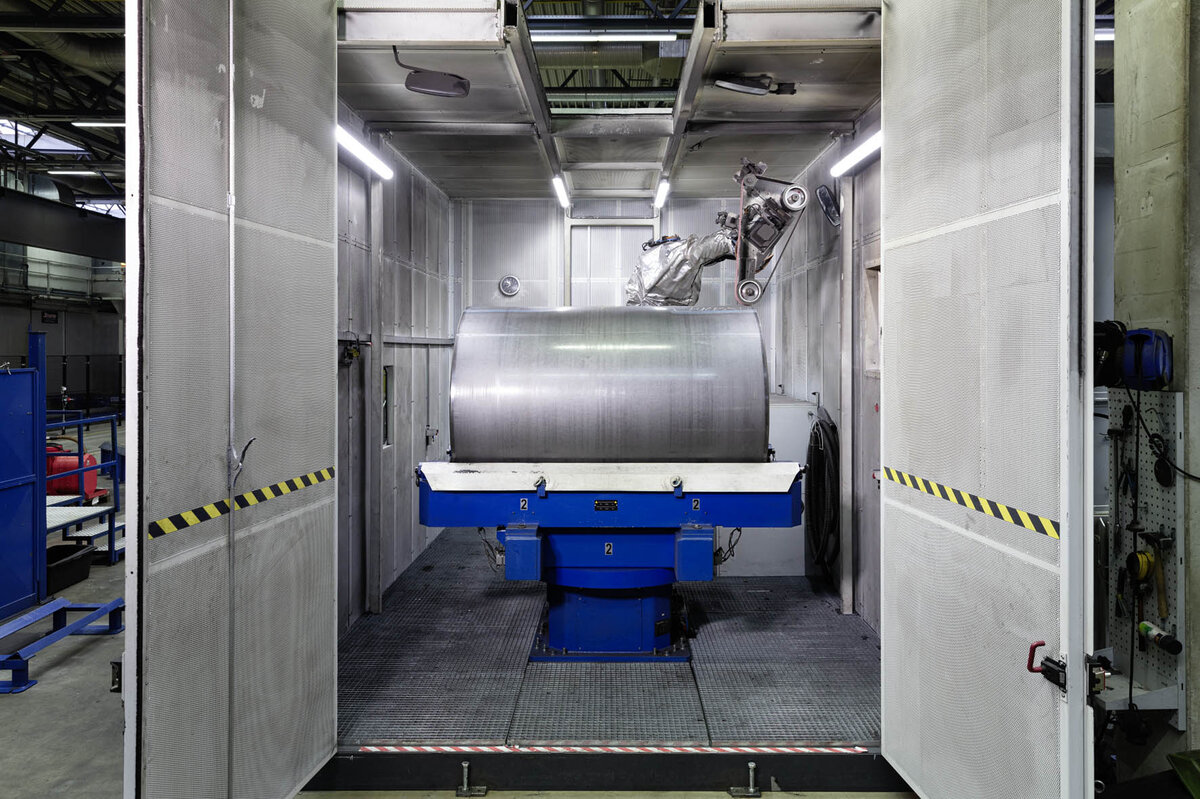
Wanted: Alternative to longitudinal seam milling
Originally a longitudinal seam milling machine took over this task. It milled off the protrusions of the weld seam in a linear movement, causing both noise and a great deal of dust. In addition, the accuracy of the process did not meet Bomag's requirements.
That is why the people in charge at Bomag were looking for an alternative to milling and also looked into robotics. This is because many processes in drum production - including material transport by heavy-duty AGVs - are already automated.
The contact to the company that finally developed and implemented the solution came about more by chance: Harald Aßmann, team leader at the drum factory, accepted the invitation to a Yaskawa in-house exhibition and informed himself about the possibilities of robot-supported grinding. The information he received convinced him: "We got to know how grinding robots were used in existing projects. This showed us, that Yaskawa is the right partner for us."
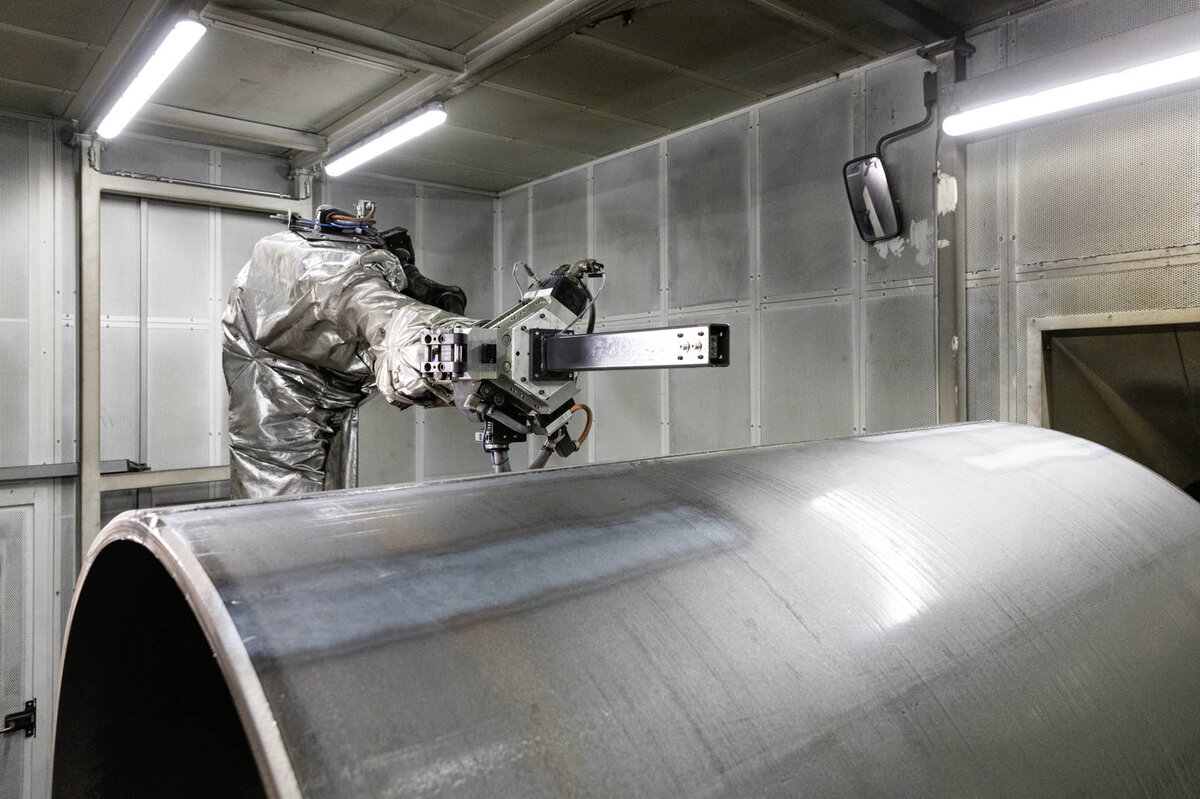
First step: Measuring the weld seam
After intensive project work, Yaskawa installed a completely enclosed system in the Bomag single drum roller production facility, in which the drum is placed by crane on a rotating device also manufactured by Yaskawa, whereby the weld seam must be in the "12:00 o'clock position".
The operator starts the program and closes the enclosure. In the meantime, the robot, a large, six-axis MOTOMAN MH180, has already removed a laser measuring device from the tool changer and is measuring the weld seam very accurately in the first step. The robot does not move linearly, but in a pendulum motion along the contour of the drum in order to record the weld seam three-dimensionally.
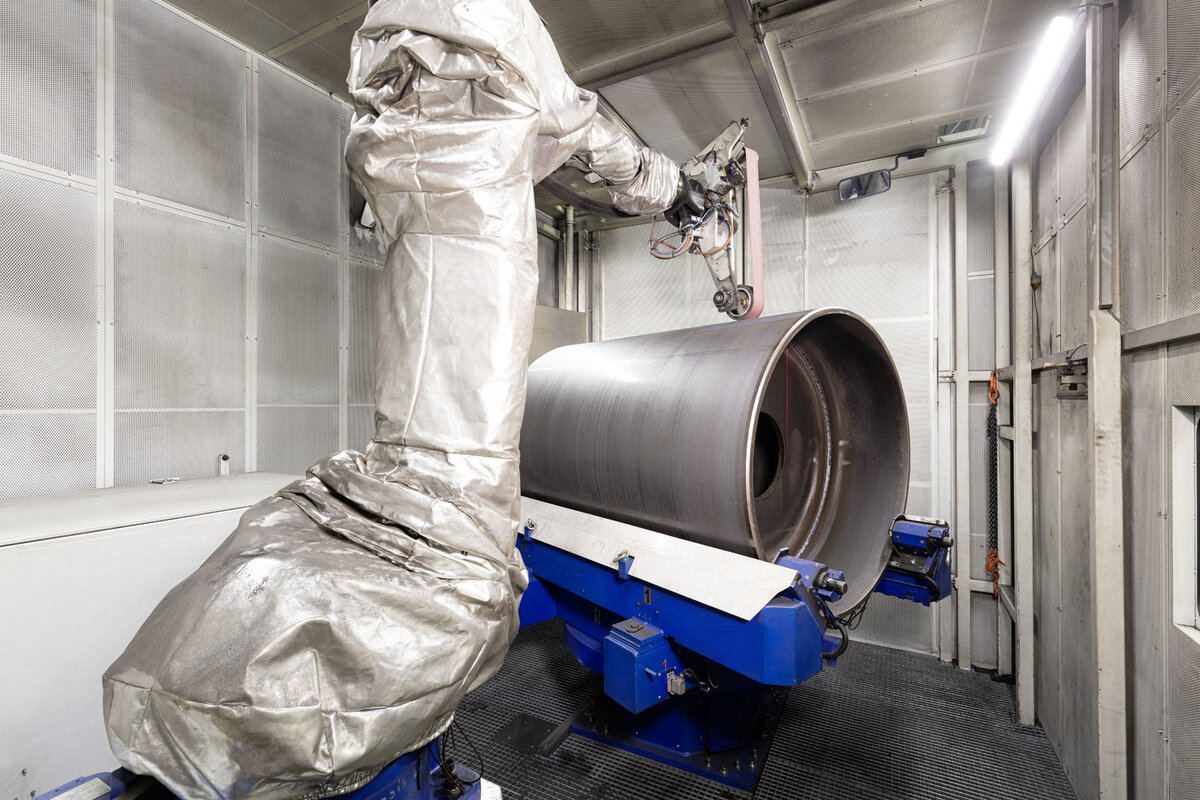
Second and third step: Grinding of longitudinal seam and side plate
The data generated by the measuring device are used as the basis for the subsequent processing step. The robot changes to a belt grinder and moves over the weld seam ten to twelve times. The current consumption of the robot serves as a parameter for the processing quality: When enough material has been removed, the grinding tool must apply less pressure and the machining process can be completed. Material is also removed at the base, i.e. at the edges of the drums.
Even during grinding, the MOTOMAN MH180 performs a non-linear movement to machine the weld seam’s complete contours. In addition, the device also rotates. Harald Aßmann: "This way we save space: Although the robot has a very long reach, it cannot cover the entire length of large roller drums"
The rotary movement is also required for the third step. Here, the powerful robot puts down the belt grinder and uses an orbital sander to polish the weld seam that joins the side plates and the outer shell of the drum. The result of the robot-assisted polishing in three steps is a perfectly flat weld seam that fits perfectly into the rounding of the drum as well as and a clean connection between the side plate and drum.
One of the special features of the "polishing robot", as it is called at Bomag, is the tool tray, protected by a lid, which only opens automatically when tools are changed. This keeps the tools clean. The MOTOMAN MH180 itself is protected from dust and flying sparks by a sheathing - a purely precautionary measure, because the powerful suction system removes almost all sparks.
Polishing without losing any time and with high flexibility
What is beneficial from the productivity point of view: This step takes place without any loss of time. Harald Aßmann: "The polishing is done parallel to the holes being drilled in the side plates." And the plant, which has been running for around six months, is also flexible. Dennis Anton, responsible for programming the cleaning robot: "So far we have written programs for almost 40 types of drums with diameters up to over two meters and different lengths.”
The Bomag managers are also satisfied with the course of the project. Small "special requests" were also taken into account on site. Dennis Anton suggested that the existing pneumatic line in the robot be used to blow out welding beads and grinding residues from the inside of the drum in the final work step.
All in all, Bomag considers the new robot to be an exemplary automation project. Harald Aßmann concludes: “We have increased our level of efficiency because our colleagues no longer have to sand and polish manually. This also reduces the physical strain on employees, who can devote themselves to more demanding tasks during this time." In addition noise and dust emissions have been reduced throughout the drum factory.