More than 100 years committed to technical progress has made us the leading manufacturer in the fields of variable AC drives, servo drives, control technology and robotics.
MOTOMAN Robot Controllers
FS100
Compact Robot Controller
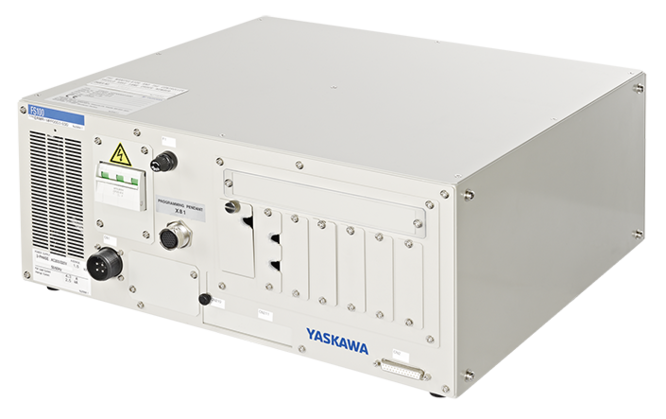
Overview
The Yaskawa FS100 is a powerful and precise, compact open robot controller, specially designed for High Speed Pick&Place and integration into packaging lines. It's small footprint and lightweight housing is ideal for space-saving stand-alone installation, or it can be installed horizontally or vertically in a machine control cabinet.
The FS100 is used in combination with MPP-Series and MPK-Series Pick&Place Robots, SIA-Series 7-axis Robots and SDA-Series Dual Arm Robots.
Operation
The FS100 controller comes with a Touch Screen Teach Pendant. The operation concept of MOTOMAN robots has been evolved and optimized over the years, based on the experience and feedback of more than 500.000 robots installed in the field so far, resulting in a today's highly efficient operating and programming environment with simple and easy-to-learn flat hierarchy menu structures, hotkeys, quick takeover of teach positions and understandable program structures with simple line based statements. Using the powerful, high level language Inform, specialists can user powerful commands, make excessive use of control logic or even create sophisticated motion or communication functions or drivers on their own.
For use with Dual Arm Robots, The FS100 provides a set of command statements and functions to make teaching and programming of synchroneous motion of both arms comfortable and easy.
Motion Control Technology
The multitasking, non-Windows-based operating system of the FS100, with very fast interpolation cycle does not require virus protection (saving the associated high update/maintenance efforts). The boot time is <40 sec.
Functions and Function Packages (Hardware/Software)
The FS100 offers a variety of functions (e.g. Servofloat, Machine Vision), all of them making programming and commissioning of MOTOMAN robots and their peripheral comfortable and easy.
Machine Safety (MSU/FSU)
The FS100 has a MSU safety system architecture (Emergency Stop and Safety Signals for safe I/O communication). The Teach Pendant provides the obligatory 3 position enabling switches. All robot servo motors are using high precision absolute encoders and spring operated brakes which are closed in the event of an emergency stop - there is no need for cyclical brake tests.
Open Communication
The FS100 can be easily integrated into existing networks. The robot controller comes with a set of standard communication interfaces, e.g. Ethernet and USB ports or digital inputs/outputs, as well as the FTP-capable TCP/IP web server function, allowing to read/set the controller status or enabling remote monitoring or maintenance over the Web.
The YRC1000micro is supporting a wide veariety of fieldbus systems, such as Ethernet-IP, Ethercat, Profinet, Profibus and CCLink. Direct or fieldbus-based communication interfaces are available for a variety of peripheral devices and equipment, often combined with a HMI integration on the teach pendant, e.g. supporting different grippers, 2D/3D Vision Systems or Force/Torque Sensors.
Downloads
Name | |||
Flyer Controller FS100
Robot Controller MOTOMAN FS100 Data sheet | English |
Data sheet | English | |
Flyer Steuerung FS100
Robotersteuerung MOTOMAN FS100 Data sheet | German |
Data sheet | German | |
FS100 3D CAD/CAE | | CAD/CAE | ||
FS100 2D CAD/CAE | | CAD/CAE |